What measures are taken to ensure consistent performance in an industrial peristaltic tube over its service life?
Ensuring consistent performance in an industrial peristaltic tube over its service life requires several measures to be taken, including:
- Material Selection: Choosing high-quality tubing materials with properties suited to the specific application is crucial. Factors such as chemical compatibility, temperature resistance, flexibility, and abrasion resistance should be considered to ensure optimal performance and longevity.
- Quality Assurance: Implementing stringent quality control measures during tubing manufacturing helps ensure uniformity and reliability. This includes monitoring material composition, dimensional accuracy, wall thickness, and surface finish to maintain consistent performance characteristics.
- Tubing Integrity Testing: Conducting integrity tests on tubing samples to identify any defects or weaknesses before installation is essential. Tests such as pressure testing, leak testing, and visual inspection can help detect flaws that could compromise performance or reliability.
- Proper Installation: Following manufacturer recommendations and guidelines for tubing installation is essential to prevent damage or deformation that could affect performance. Proper alignment, secure attachment, and adequate support help maintain tubing integrity and ensure consistent fluid flow.
- Regular Maintenance: Implementing a regular maintenance schedule to inspect and replace tubing as needed helps prevent unexpected failures and ensures continuous performance. Monitoring tubing condition, checking for signs of wear or deterioration, and replacing worn-out tubing in a timely manner are critical preventive maintenance practices.
- Monitoring and Control Systems: Integrating monitoring and control systems into the pump setup allows for real-time monitoring of tubing condition and performance parameters. This enables early detection of issues such as tubing wear,peristaltic tube fatigue, or blockages, allowing for proactive maintenance and minimizing downtime.
- Fluid Compatibility Considerations: Ensuring that the tubing material is compatible with the fluid being pumped helps prevent chemical degradation, swelling, or contamination that could affect performance over time. Conducting compatibility tests and selecting tubing materials resistant to chemical attack ensures consistent performance in challenging fluid handling applications.
- Operating Conditions Optimization: Adjusting operating parameters such as speed, pressure, and temperature within recommended limits helps minimize stress on the tubing and extend its service life. Avoiding excessive flow rates, pressure spikes, or temperature extremes helps preserve tubing integrity and maintain consistent performance.
- Training and Education: Providing training and education to personnel responsible for tubing installation, operation, and maintenance helps ensure proper handling and care. Awareness of best practices, troubleshooting techniques, and potential failure modes enables proactive management of tubing performance and longevity.
By implementing these measures, industrial operators can ensure consistent performance in peristaltic tubing over its service life, maximizing reliability, efficiency, and uptime in fluid handling applications.
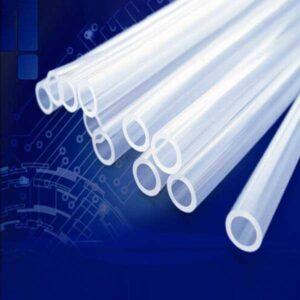
Comments are closed.